A solution to the permalloy problem
Abstract
We propose a solution to the longstanding permalloy problem—why the particular composition of permalloy, , achieves a dramatic drop in hysteresis, while its material constants show no obvious signal of this behavior. We use our recently developed coercivity tool to show that a delicate balance between local instabilities and magnetic material constants are necessary to explain the dramatic drop of hysteresis at 78.5 Ni. Our findings are in agreement with the permalloy experiments and, more broadly, provide theoretical guidance for the discovery of novel low hysteresis magnetic alloys.
Introduction
In the early 20th century, an Fe-Ni alloy with unusually low coercivity was discovered at Bell Laboratories [1]. This magnetic alloy with precisely Ni, now known as permalloy, demonstrated a drastic lowered hysteresis, quantified by the value of coercivity, relative to nearby alloys, see Fig. 1(a-c). Several researchers attribute the dramatic decrease in hysteresis at Ni to its small anisotropy constant – a material constant that quantifies the difficulty of rotating the magnetization away from certain preferred crystallographic axes [2]. However, a closer examination of the binary Fe-Ni alloys, containing Ni, shows several peculiarities in behavior that contradict our current understanding of the origins of magnetic hysteresis. For example, the anisotropy constant of the FeNi alloy is zero at Ni; however, there is not even a local minimum of the coercivity vs. composition at this Ni-content. However, at Ni, where the anisotropy constant is clearly not zero, the coercivity is minimized [3] (see supplementary information).
Besides the anisotropy constant, researchers have suspected that the magnetostriction constants,111These material constants relate the preferred strains corresponding to a given magnetization. and , play some role in lowering magnetic hysteresis [12, 13, 9]. The potential influence of is supported by the presence of the second permalloy composition at Ni, where the coercivity vs. composition shows a diffuse local minimum, not nearly as sharp as in Ni, but still clearly noticeable, see Fig. 1(a,c). The values of anisotropy constant and magnetostriction constant are far from zero at Ni, but the magnetostriction constant vanishes precisely at this composition. Following this line of argument, we would expect to see a lowering of hysteresis at and Ni, at which the magnetostriction constants and are zero, respectively. However, there is not even a discernible local minimum of coercivity vs. composition at these compositions. By contrast, as mentioned above, the magnetic hysteresis is minimum at Ni at which neither of the magnetostriction constants nor the anisotropy constant are zero. This collection of apparently contradictory facts is known as the permalloy problem [3].
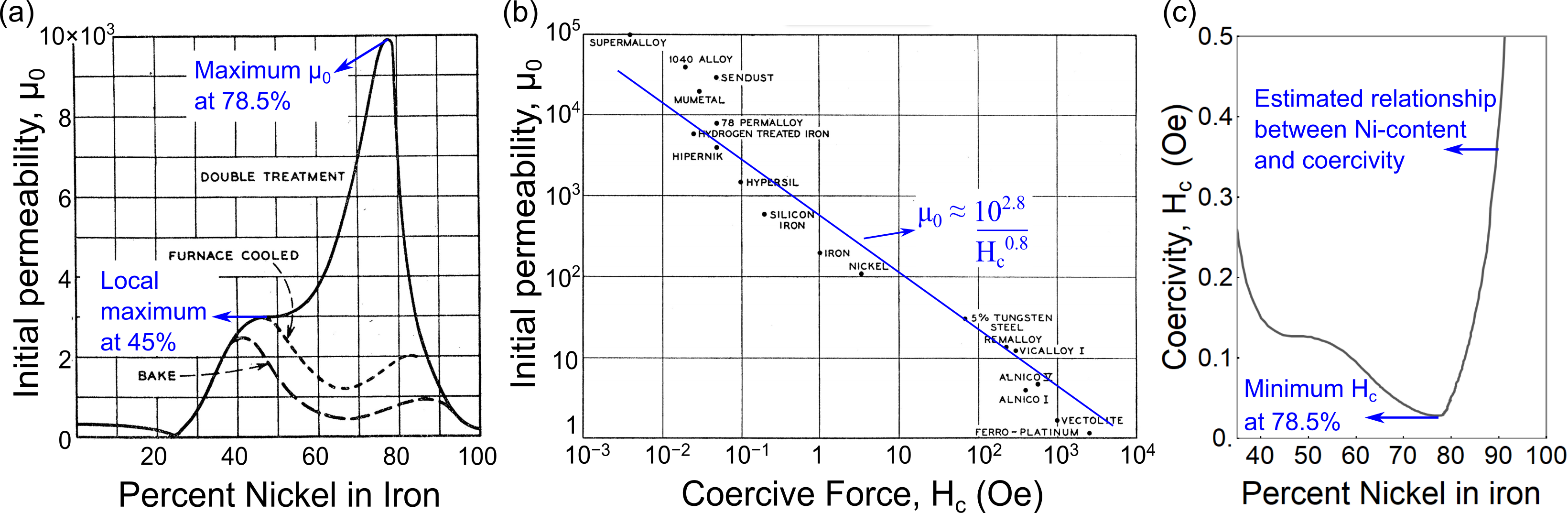
Processing also has an important influence on hysteresis. For example, slow cooling can raise the composition of lowest hysteresis to higher Ni content [2]. Typically, the effect of a thermo-mechanical treatment in the Fe-Ni system is to induce the formation of precipitates. This in turn has two main effects: (a) it leads to the preferential deposition of one element into precipitates, which have a very different composition than the matrix. This precipitation causes a departure of the matrix composition from the nominal composition; and (b) it develops residual stress due to the geometric incompatibility of the precipitate and the matrix. This geometric incompatibility induces coherency stresses that affect magnetic properties via magnetostriction [4, 5]. In certain systems more disruptive processing treatments, such as rapid solidification leading to nanocrystalline materials, is also a productive route toward extremely low hysteresis materials [6, 7, 8].
Researchers have attempted to resolve the permalloy problem for many years [3, 12, 9]. Domain theory has been used to explain the ease of domain rotation and domain wall movement at small values of anisotropy and magnetostriction constants [12, 13]. These calculations make certain assumptions on microstructures and domain structure, and do not lead to the permalloy composition. In another study [9], the criterion between magnetostriction and anisotropy constants (in the presence of residual stresses ) is proposed as governing coercivity. While we agree with the importance of accounting for in predicting coercivity, we do not see a fundamental theoretical or experimental basis for this criterion. In addition, since residual stress is a tensor varying with position in a heterogeneous solid, it is not clear to us how to use this criterion. Several recent studies examine effect of grain orientation and crystallographic texture on coercivity in FeNiMo alloys [14, 15], however these studies do not address how fundamental material constants interact with defects and residual stress to lower hysteresis in this system.
In our paper, while recognizing that processing can be highly influential, we explore the hypothesis that there is a relation between hysteresis and fundamental material constants in the FeNi system. Doing so, we shed light on the permalloy problem.
Recently, we developed a coercivity tool based on the micromagnetics theory [24]. Our tool differs from other theoretical methods that predict magnetic coercivity [18, 20], in two ways: (a) First, we account for magnetoelastic interactions that have been neglected in most prior studies. (b) Second, we introduce an optimized localized disturbance in the form of a spike-domain microstructure that grows during magnetization reversal. By introducing the localized disturbance, we capture the delicate balance between magnetic material constants that govern hysteresis, and predict coercivity with greater accuracy than other methods based on linear stability analysis. In this work, we apply this coercivity tool to provide insight into the permalloy problem.
In this paper, we first provide an overview of the micromagnetics theory used in our coercivity tool. We then apply this tool in two studies on iron-nickel alloys: In Study 1, we test the hypothesis that a specific combination of magnetoelastic constants (with residual stress) and anisotropy constants is necessary to lower the coercivity at the permalloy composition. Here, we compute coercivity in iron-nickel alloys in two cases, (a) by accounting for magnetostrictive effects and (b) by ignoring all magnetoelastic energy contributions. In Study 2, we test the hypothesis that neither defect geometry nor defect orientation significantly affect the combination of material constants at which the lowest coercivity is achieved. Finally, we compare the magnetic coercivity predicted by the present study with previously proposed ideas [12, 13]. Our simulations show that the lowest coercivity is attained at Ni-content when magnetoelastic energy is accounted in the model, and provides insight into minimum coercivity values of other Fe-Ni alloys.
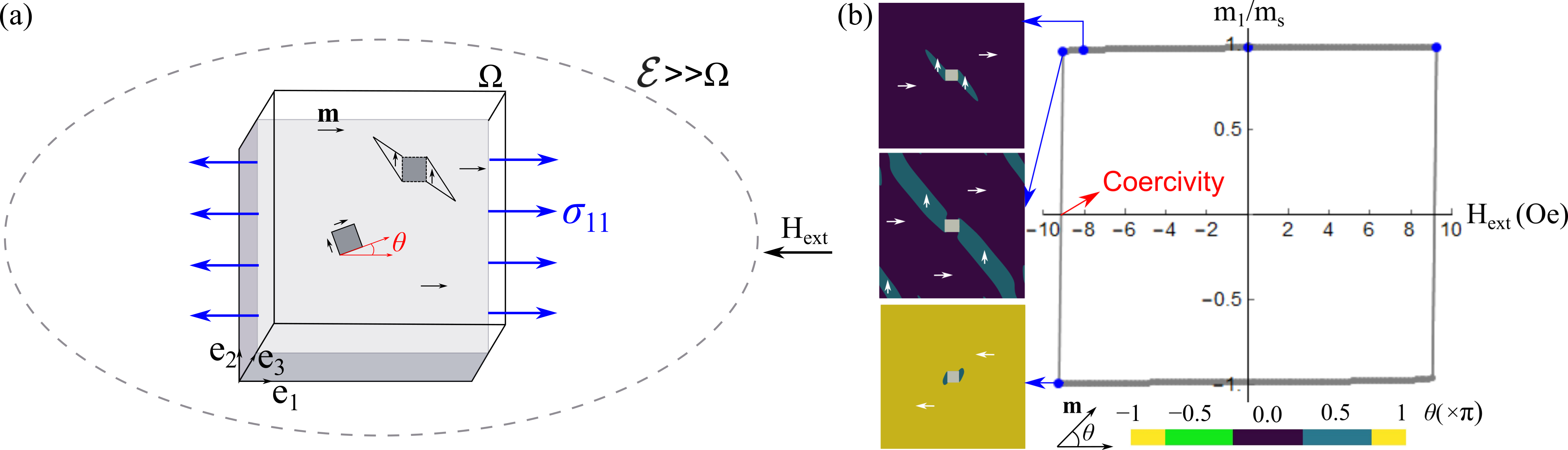
Theory and Methods
Our coercivity tool is based on micromagnetics with magnetostriction [16, 17]. The total free energy is a functional of magnetization , , and strain given by
(1) |
and are the (constant) applied stress and magnetic field, respectively. Here, the anisotropy energy penalizes rotation of the magnetization away from the easy axes, the elastic energy penalizes mechanical deformation away from the preferred strain, defined by
(5) |
Finally, the vector field is the stray field generated by the magnetization distribution, and the magnetostatic energy is the energy required to assemble a collection of elementary magnetic dipoles into the given magnetization distribution [19]. The stray field is obtained by solving the magnetostatic equation on all of space. Here, we note that in this model the five material constants together with the elastic modulus tensor (depending on the three moduli ) and applied field and stress determine the form of the micromagnetic energy. See [24] for further explanation.
We compute the evolution of the magnetization using a local energy minimization technique, based on the generalized Landau-Lifshitz-Ginzburg equation [21]:
(6) |
Here, is the effective field, is the gyromagnetic ratio, and is the damping constant. We numerically solve Eq. 6 using the Gauss Siedel Projection method [22], and identify equilibrium states when the magnetization evolution converges, . At each iteration we compute the magnetostatic field and the strain by solving their respective equilibrium equations:
(7) | ||||
(8) |
The magnetostatic equilibrium condition arises from the Maxwell equations, namely and . We compute the magnetostatic and mechanical equilibrium conditions in Eqs. 7-8 in Fourier space [23]. Further details on the numerical method can be found in Refs. [24, 23, 22]
In the present work, we calibrate our micromagnetics model for the FeNi alloy as a function of Ni-content. The material constants used in our calculations are listed in the supplementary material. We assume an oblate (pancake-like shaped) ellipsoid under a suitably oriented applied field, see Fig. 2(a).222The applied field is directed along the major axis of the magnetic ellipsoid. The easy axes for a magnetic body with anisotropy constants and are along and crystallographic directions, respectively. This ellipsoid is uniformly magnetized except at the proximity of defects. Using a computational scheme based on the ellipsoid and reciprocal theorems333In our method the presence of the large ellipsoidal body is essential as a way of describing the poles on the boundary of the macroscale body without having to simulate the external fields due to these poles. See Ref. [24]., we model a 3D computational domain with a nonmagnetic inclusion at its geometric center. The domain and the inclusion are of sizes and grid points. The cell size is chosen such that the domain walls span across 3-4 elements. The magnetization inside the inclusion is held at zero throughout the computation, . Outside the defect, we initialize the computation domain with a uniform magnetization and apply a large external field along the easy axes, , see Fig. 2(b). As we decrease the applied field the spike domain at first grows slowly until a critical field is reached at which the magnetization vector reverses abruptly. We identify this value of the applied field with coercivity. We use this approach to predict coercivity of the iron-nickel alloys as a function of Ni-content.
Results
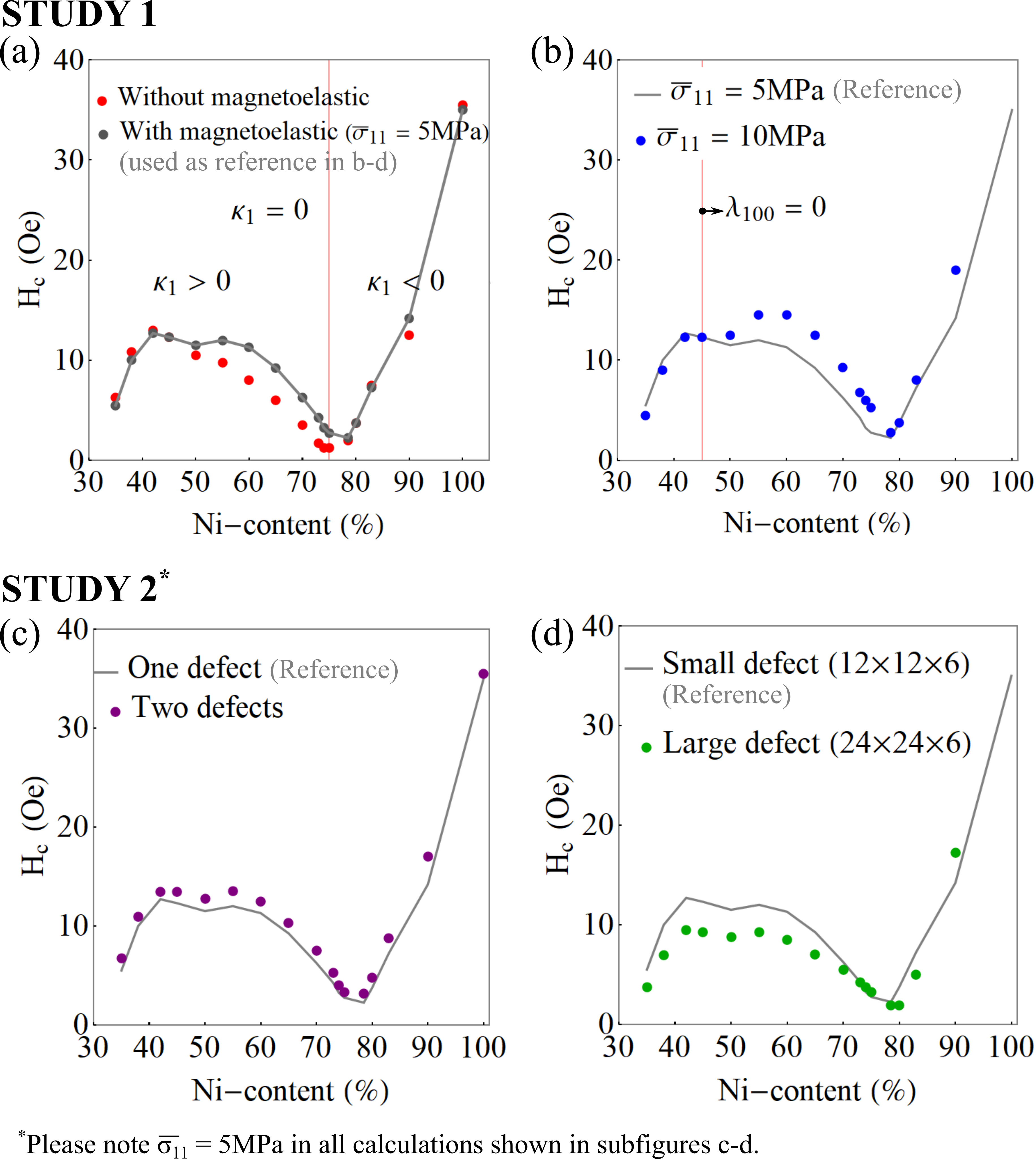
In Study 1, we test our hypothesis that the magnetoelastic energy contributions (e.g., magnetostrictive and residual stress), in addition to the anisotropy energy, are necessary to reproduce the characteristic features of coercivity vs. composition in iron-nickel alloys. To test this hypothesis, we compute the coercivity for iron-nickel alloys in two cases: (a) by accounting for the magnetoelastic energy with a small residual stress , and (b) by ignoring all magnetoelastic energy in Eq. 1. Note that a residual stress of corresponds to a uniaxial strain of about 25 (with typical Young’s Modulus of about ) for FeNi alloys. As noted above, these residual stresses naturally arise from precipitation during heat treatment, and from other defects such as the presence of grain boundaries and, in particular, triple junctions. For example a temperature change of 1K causes about strain in iron. Our assumption of residual strains is well within the thermal strain for moderate temperature changes.
Fig. 3(a) shows the coercivity of iron-nickel alloys for the two cases. In line with the experimental evidence, the coercivity is the lowest at Ni-content when both magnetoelastic and anisotropy energy contributions are accounted in the free energy function. When magnetoelastic energy is neglected (or small), the coercivity is minimum at Ni-content at which . Similarly, our calculations show that the coercive field has a local minimum at Ni-content, when both magnetoelastic and anisotropy energy contributions are included in the model. Furthermore, this minima is more pronounced with increased stresses in the material, see Fig. 3(b). Although the anisotropy constant is large in this composition range , we find that its coercivity is relatively small in this neighborhood. This is consistent with previous hypotheses by researchers [3, 10], who speculated that the low magnetostriction constant in the neighborhood causes a local minimum (or maximum) in the FeNi coercivity (or permeability) plot. When the strain values are decoupled from the magnetization vector, and consequently the residual stresses do not affect the coercivity values.
In Study 2, we test our hypothesis that neither defect geometries nor defect densities affect the balance between material constants at which minimum coercivity is achieved. Fig. 3(c-d) shows the effect of defect geometry (such as orientation and shape) and density on the coercivity of the FeNi alloy. Note, these computations were modelled with a residual stress of . The magnitude of the coercivity is sensitive to defect geometries and tensile stresses, however, as hypothesized, for a given defect configuration the minimum coercivity remains at Ni-content. The balance between anisotropy and magnetostriction constants that minimizes the coercivity at Ni-content is not significantly affected by the changes in defect geometry and/or orientation. These results are consistent with a wider set of variations of defect size and placement presented in [24] (but not for material constants of permalloy).
We next compare our findings with predictions from Domain Theory and Lewis criterion [12, 13, 9]. We do not include results from linear stability analysis of the single domain state based on micromagnetics, because these vastly over predict the coercivity.444This over prediction is known as the “coercivity paradox”. Our simulations are outside the regime of linear stability analysis. We compare our results with prior predictions by choosing specific compositions of the iron-nickel alloys (e.g., alloys with 45,75,78.5,80, and 83 Ni-content) to highlight the zeros of the material constants (see supplementary information): We note that the formulae from Domain Theory or predicts large permeabilities at multiple singularities, however, they fail to identify the highest permeability (lowest coercivity) at the Ni-content alloy. For example, Domain Theory predicts the highest permeability at Ni-content with and at Ni-content with , however, experiments indicate that the highest permeability occurs at 78.5 Ni-content at which neither nor are zero. Similarly, the Lewis criterion is closely satisfied at Ni-content with a value , however, it misses the dramatic drop in coercivity at the alloy composition. Furthermore, it is unclear on how to choose the residual stress in the criterion; we keep it at to reflect the fact that the measured values were obtained from alloys with nominally the same heat treatment. By contrast, our coercivity tool predicts the highest permeability (or lowest coercivity) at Ni-content, see Fig. 3(a-b). Furthermore, it shows a local minimum in coercivity at Ni, and provides insight into coercivities at other alloy compositions with zero material constants. Overall, the prior criteria or formulae that explain the low coercivity at the permalloy composition are not general, and do not fully explain the singularities at other material compositions. These results suggest that our approach based on non-linear stability analysis at the shoulder of the hysteresis loop together with a delicate balance of magnetic material constants is a potential way forward to reliably predict coercivities.
Discussion
In summary, our findings on coercivity as a function of Ni-content in the binary FeNi alloys show that the lowest coercivity is attained at Ni-content. This was the case in Study 1 when both anisotropy and magnetoelastic energy contributions were included in the calculations. In Study 2, although tensile stresses and defect geometries affected the coercivity values, the minimum coercivity was still observed at Ni-content. Furthermore, our predictions on coercivity as a function of Ni-content are more accurate than prior criterion based on domain theory, and provides insight into the permalloy problem. Below, we discuss some limiting conditions on our results and then highlight the key features of our work.
Two features of this work limit the conclusions we can draw about the permalloy problem. First, we assume a single crystalline ellipsoid body, which does not contain grain boundaries, sharp edges and other imperfections, which are commonly found in bulk magnetic materials. This assumption possibly contributes to about an order of magnitude difference between our predicted coercivity values and those reported from experiments. Second, we model the local disturbance (spike-domain) explicitly by defining a potent defect on the computational domain. Whether developing a more fundamental theory of nucleation in the Calculus of Variations without explicitly defining the nucleus would provide further insights into magnetic coercivity is an open question. With these reservations in mind we next discuss our findings on the permalloy problem.
The key feature of our work is that we show a delicate balance between material constants, , is necessary for the low coercivity at Ni-content. This finding contrasts with some reports in the literature in which the small anisotropy constant is considered to be the factor responsible for lowering hysteresis. Although lowers the coercivity (e.g., at Ni-content), we find that magnetostriction plays an important role in governing magnetic hysteresis. Furthermore, our findings are consistent with previous hypotheses that the zero magnetostriction constants—along the easy axes—at and Ni-contents help lower the coercivity values. Despite the large anisotropy constants at these compositions, we find that their coercivities are relatively small in their local Ni-content neighbourhoods.
Another feature of our work is that we propose a theoretical method to compute coercivity, on the shoulder of the hysteresis loop, by accounting for localized instabilities (spike domain). This approach of computing non-linear stability analysis helped us to elucidate the role of magnetic material constants on coercivity. We believe that this method helped us to predict coercivities more accurately when compared to other methods that are based on linearization. In our future work, we use our tool to compute coercivity in a broader material parameter space [25], and seek to identify the fundamental relation between the material constants that governs hysteresis.
Conclusion
To conclude, the present findings contribute to a more nuanced understanding of how material constants, such as anisotropy and magnetostriction constants, affect magnetic hysteresis. Specifically, magnetoelastic interactions have been regarded to play a negligible role in lowering the coercivity. Given the current findings, we quantitatively demonstrate that the interplay between anisotropy energy, magnetoelastic energy, and localized disturbance (spike domain) is necessary to lower magnetic hysteresis. Our theoretical model serves as a design tool to discover novel combinations of material constants, which lower the coercivity in magnetic alloys.
Acknowledgment. The authors acknowledge the Minnesota Supercomputing Institute at the University of Minnesota (Dr. David Porter), and the High-Performance Computing Center at the University of Southern California for providing resources that contributed to the research results reported within this paper. The authors thank NSF (DMREF-1629026) and ONR (N00014-18-1-2766) for partial support of this work. R.D.J and A.R.B, respectively, also acknowledge the support of a Vannevar Bush Faculty Fellowship and a Provost Assistant Professor Fellowship.
References
- [1] Arnold, H.D. and Elmen, G.W., 1923. Permalloy, an alloy of remarkable magnetic properties. Journal of the Franklin Institute, 195(5), 621-632.
- [2] Bozorth, R.M., 1993. Ferromagnetism (p. 992).
- [3] Bozorth, R.M., 1953. The permalloy problem. Reviews of Modern Physics, 25(1), 42.
- [4] Fidler, J. (1982). Coercivity of precipitation hardened cobalt rare earth 17: 2 permanent magnets. Journal of magnetism and magnetic materials, 30(1), 58-70.
- [5] Sagawa, M., Okada, M., & Henmi, Z. (1976). The Relation between Precipitation and Coercivity in Co-Fe-Nb Semihard Magnetic Alloy. Transactions of the Japan Institute of Metals, 17(10), 615-619.
- [6] Jiménez-Villacorta, F., Marion, J. L., Oldham, J. T., Daniil, M., Willard, M. A., & Lewis, L. H. (2014). Magnetism-structure correlations during the transformation in rapidly-solidified MnAl nanostructured alloys. Metals, 4(1), 8-19.
- [7] McHenry, M. E., Willard, M. A., & Laughlin, D. E. (1999). Amorphous and nanocrystalline materials for applications as soft magnets. Progress in materials Science, 44(4), 291-433.
- [8] Rial, J., Villanueva, M., Céspedes, E., López, N., Camarero, J., Marshall, L. G., … & Bollero, A. (2017). Application of a novel flash-milling procedure for coercivity development in nanocrystalline MnAl permanent magnet powders. Journal of Physics D: Applied Physics, 50(10), 105004.
- [9] Lewis, B., 1964. The permalloy problem and anisotropy in nickel iron magnetic films. British Journal of Applied Physics, 15(5), p.531.
- [10] James, R. D. (2015). Magnetic alloys break the rules. Nature, 521(7552), 298-299.
- [11] Suzuki, K., Herzer, G., and Cadogan, J. M. (1998). The effect of coherent uniaxial anisotropies on the grain-size dependence of coercivity in nanocrystalline soft magnetic alloys. Journal of magnetism and magnetic materials, 177, 949-950.
- [12] R. Becker and W. Doring (1939). "Ferromagnetismus". J. W. Edwards, Ann Arbor, Michigan
- [13] Kittel, C. and Galt, J.K., 1956. Ferromagnetic domain theory. In Solid state physics (Vol. 3, pp. 437-564). Academic Press.
- [14] Mohamed, A. E. M. A., Zou, J., Sheridan, R. S., Bongs, K., and Attallah, M. M. (2020). Magnetic shielding promotion via the control of magnetic anisotropy and thermal Post processing in laser powder bed fusion processed NiFeMo-based soft magnet. Additive Manufacturing, 32, 101079.
- [15] Zou, J., Gaber, Y., Voulazeris, G., Li, S., Vazquez, L., Liu, L.F., Yao, M.Y., Wang, Y.J., Holynski, M., Bongs, K. and Attallah, M.M. (2018). Controlling the grain orientation during laser powder bed fusion to tailor the magnetic characteristics in a Ni-Fe based soft magnet. Acta Materialia, 158, 230-238.
- [16] Brown, W.F., 1963. Micromagnetics (No. 18). interscience publishers.
- [17] Brown, W.F., 1966. Magnetoelastic interactions (Vol. 9). Berlin: Springer.
- [18] Kruzík, M., and Prohl, A., (2006). Recent developments in the modeling, analysis, and numerics of ferromagnetism. SIAM Review, 48(3), 439-483.
- [19] James, Richard D and Müller, Stefan (1994). Internal variables and fine-scale oscillations in micromagnetics. Continuum Mechanics and Thermodynamics 6(4), 291-336.
- [20] Lopez-Diaz, L., Aurelio, D., Torres, L., Martinez, E., Hernandez-Lopez, M.A., Gomez, J., Alejos, O., Carpentieri, M., Finocchio, G. and Consolo, G., 2012. Micromagnetic simulations using graphics processing units. Journal of Physics D: Applied Physics, 45(32), 323001.
- [21] Gilbert, T. L. (2004) A phenomenological theory of damping in ferromagnetic materials, in IEEE Transactions on Magnetics 40(6), 3443-3449, doi: 10.1109/TMAG.2004.836740.
- [22] Wang, X.P., Garcia-Cervera, C.J. and Weinan, E., 2001. A Gauss-Siedel projection method for micromagnetics simulations. Journal of Computational Physics, 171(1), 357-372.
- [23] Zhang, J.X. and Chen, L.Q., 2005. Phase-field microelasticity theory and micromagnetic simulations of domain structures in giant magnetostrictive materials. Acta Materialia, 53(9), 2845-2855.
- [24] Renuka Balakrishna, A. and James R. D., 2020. A tool to predict coercivity in magnetic materials. Under revision, arXiv preprint arXiv:2012.09320.
- [25] Renuka Balakrishna, A. and James R. D. A search for magnetic alloys with low hysteresis. Preprint.
Supplementary information
Table 1 shows the magnetic material constants, namely the anisotropy constant , the magnetostriction constants , and the saturation magnetization , of FeNi alloys used in this calculation. The elastic moduli are , , and .
Ni | (kJ/m3) | () | () | |
---|---|---|---|---|
35 | 0.462 | -5.85 | 16.9 | 0.94 |
38 | 0.889 | -7.30 | 25.5 | 1.13 |
42 | 1.140 | -3.89 | 32.3 | 1.23 |
45 | 1.100 | 0.0 | 32.8 | 1.26 |
50 | 0.958 | 10.0 | 30.9 | 1.25 |
55 | 0.847 | 20.9 | 26.8 | 1.19 |
60 | 0.701 | 26.2 | 22.2 | 1.15 |
65 | 0.500 | 25.6 | 16.5 | 1.07 |
70 | 0.287 | 22.3 | 10.7 | 0.99 |
73 | 0.142 | 18.9 | 7.13 | 0.94 |
74 | 0.052 | 18.5 | 6.29 | 0.92 |
75 | 0.000 | 17.2 | 5.46 | 0.90 |
77 | -0.084 | 14.5 | 3.68 | 0.87 |
78.5 | -0.161 | 11.8 | 1.91 | 0.84 |
80 | -0.273 | 8.45 | 0.0 | 0.82 |
83 | -0.520 | 0.0 | -2.68 | 0.76 |
90 | -1.600 | -23.2 | -10.8 | 0.64 |
100 | -5.880 | -53.1 | -26.5 | 0.48 |